Eternalwater Filtration’s Interpretation of Sterile Filtration Technology and Application Guide
2024-09-05 Eternalwater
Sterile filtration is widely used in the pharmaceutical industry, and in the manufacture process of sterile medicinal products, especially for non-terminally sterilized products, it mainly relies on sterile filtration and aseptic manufacture process to meet the requirements of aseptic controlling. GMP guidelines issued by various regulatory agencies are all required process validation for medicinal product manufacturing to prove that the filters used meet the established requirements for use. As a manufacturer specializing in the production of sterilizing filter cartridges, Eternalwater Filtration shares a detailed interpretation of sterile filtration technology and application.
1.About Validation of Sterile Filtration
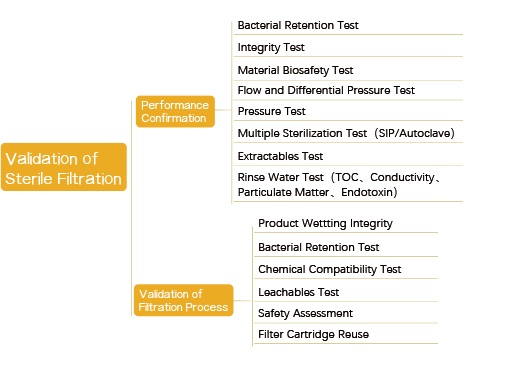
The performance confirmation of the sterilizing filter is generally completed by the filter manufacturer; The validation of the sterile filtration process can be completed by the user or a commissioned testing organization (e.g., the manufacturer of the filter or a third-party laboratory), but the filter user should ultimately ensure that the operating parameters and permissible extremums in the actual manufacture process have been covered and documented accordingly.
Brief Summary:
1. The validation documents of different filter manufacturers are generally not substituted for each other, and the validation documents of sterile filtration of the same material and the same manufacturer can often not directly interchanged, unless there is a reasonable statement or supportive document.
2. If there are two or more different manufacturers in the manufacture process who provide filters of the same material or different materials, or filters of the same materials (different membrane forming processes) from the same manufacturer, the validation should be carried out separately. This is because the structures of the membrane may not be exactly the same due to different membrane forming processes and different additives.
2. Bacterial Retention Test
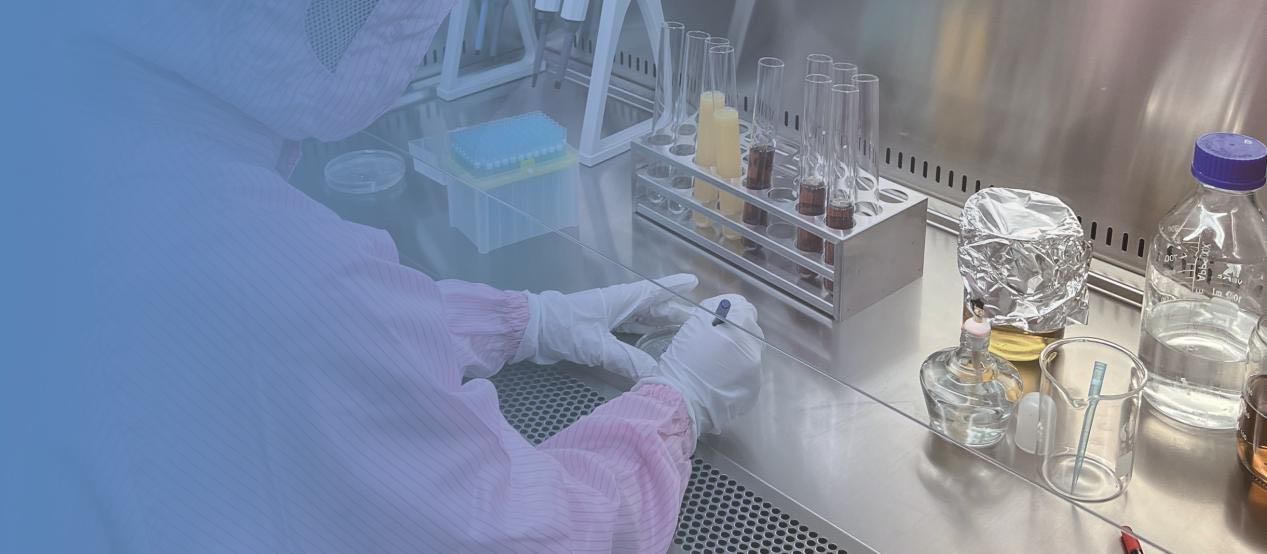
The purpose of the bacterial retention test is to simulate the worst conditions in the actual manufacture filtration process (the higher the filtration temperature, the longer the filtration time, the larger the batch, and the higher the differential pressure, the closer it’s to the worst conditions), and to filter the product solution or product substitute solution containing a certain amount of challenging microorganisms to confirm the microbial retention capacity of the sterilizing filter. Before the bacterial retention test, the activity test (survivability test) is conducted to confirm the survival of the challenged microorganisms in the medicinal product under process conditions to determine a reasonable bacterial challenge method.
Brief Summary:
1. B.diminuta is a standard challenge microorganism for bacterial retention test in validation of sterile filtration.
2. Microbial retention test generally consists of three batches, at least one of which should be a low bubble point (low specification) filter membrane.
3. Low bubble point requirement: close to within 10% of the standard bubble point value.
4. If a low bubble point filter membrane is not used in validation, the bubble point value of standard solution membrane/filter cartridge in the actual manufacture process must be higher than the minimum bubble point value of the membrane actually used in the validation test.
5. Set up a 0.45μm parallel control.
6. Challenge microorganism should be directly inoculated into the medicinal product for bacterial challenge as much as possible.
7. If an alternative solution is used for the test, reasonable data and interpretation need to be provided.
8. For the same product, that is, products with the same components but different concentrations, the method of challenging the limit concentration can be used in validation.
3. Extractables and Leachables Test
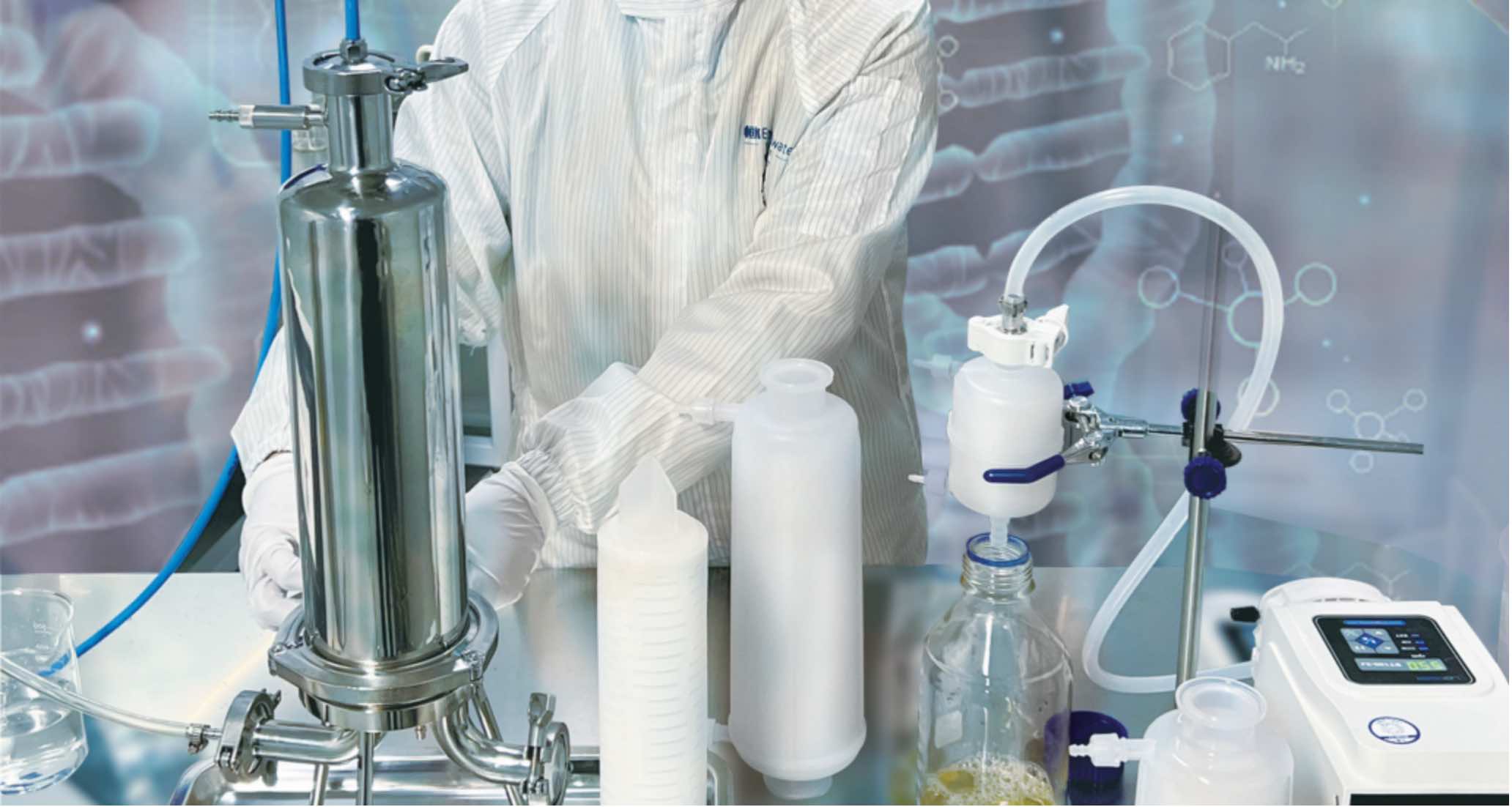
Extractables: Refers to the chemical components that may be extracted from contact surfaces through the simulated or more demanding forces (e.g., solvent, temperature, or time), which is determined under simulated solvent and "worst" conditions. (Worst conditions such as model solvent selection, conditions and parameters for sterilization , highest filtration temperature, and longest contact time.) )
Leachables: Chemicals and elements that migrate from contact material or component of any product to the process fluid under actual process conditions and may be present in the final product. Leachables are usually a subset of extractables and may also be reaction products or degradation products of extractables.
Brief Summary:
1. The data of extractables under worst conditions should be obtained first and be used to evaluate the safety of the medicinal product. Extractables reflect the greatest potential for leachables, and the test and evaluation of extractables are both important regardless of whether an extractables test is conducted or not.
2. The model solvent used for test should be able to simulate the actual prescription and should not have chemical compatibility issues with the filter. It should generally have the same or similar physical and chemical properties as the product, such as pH, polarity or ionic strength, etc.
3. Using longest filtration time, highest filtration temperature, maximum number of steam sterilization cycles and increasing the number and dosage of gamma radiation may all improve the level of extractables.
4. The extractables test should be completed using sterilized filters. The filters used for the test should not be pre-flushed as much as possible.
5. The extractables and leachables test requires a combination of qualitative and quantitative methods.
6. After completing the extractables or leachables test, the safety assessment of the results should be carried out according to the type and content of the filter extractables or leachables, combined with the concentration, dosage, dosing time and dosing route in the final dosage form of medicinal product, so as to evaluate whether the extractables and leachables have safety risks.
4. Chemical Compatibility Test
The purpose of the chemical compatibility test is to evaluate the chemical effect of the medium to be filtered on the filtration device under specific process conditions.
Brief Summary:
1.The chemical compatibility test should cover the entire filtration device, not only the filter membrane, but also the housing and skeleton, sealing ring, and supporting diversion layer.
2. The worst process conditions, filtration flow rate, contact time, temperature, etc. should be considered.
3. The chemical compatibility test items generally include: visual inspection of the filter before and after contacting with the medium to be filtered; changes in flow rate during filtration; changes in weight/ thickness of filter membrane ; Changes in integrity test values such as bubble point before and after filtration; changes in the tensile strength of the filter membrane; filter membrane scanning electron microscopy (SEM) confirmation, etc.
5. Adsorption Test
1. The process by which certain components of the medium to be filtered adhere to the filter, it may affect the composition and concentration of the medium to be filtered.
2. The adsorptive materials in the filter include the filter membrane, housing and supporting material. Factors such as flow rate, filtration time, concentration of medium to be filtered, concentration of preservatives, temperature and pH value may affect the adsorption effect.
6.Integrity Test Based on Product
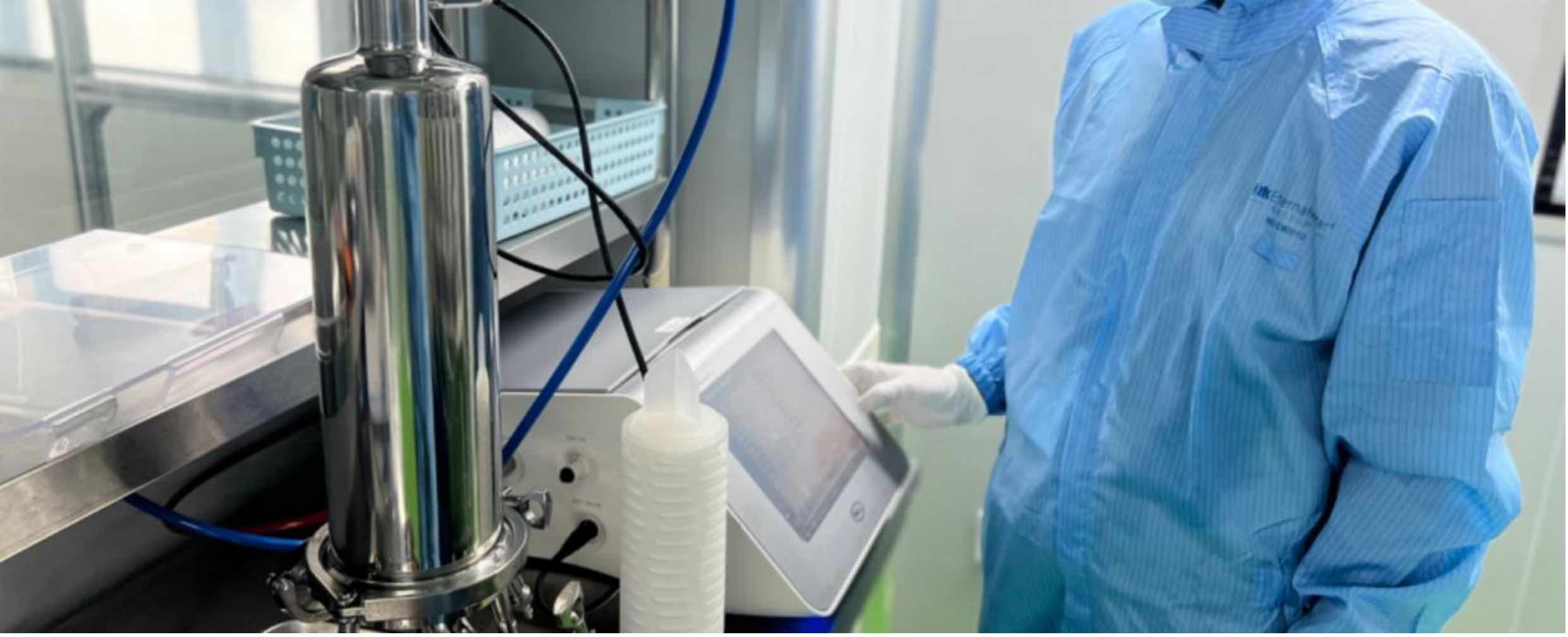
1. The wetting medium for the integrity test of the filter after use should be specified.
2. If liquid medicine is adopted as the wetting medium, the validation of the integrity standard of the product should be carried out to support the determination of the standard.
3. Scaled-down study conducted at the lab scale is the first part of product integrity test. The second part is to periodically monitor the bubble point or trend of the product diffusion flow under actual process conditions as a part of the validation.
7. Revalidation
After completing the validation of the filtration process, the product properties and process conditions should be evaluated regularly to determine if revalidation is required.
At least (but not limited to) evaluate the following to decide if revalidation is required:
1. The flow rate per unit area is higher than the validated flow rate
2. The filtration differential pressure exceeds the validated differential pressure
3. The filtration time exceeds the validated time
4. Increase the filtration capacity while the filtration area remains the same
5. Change of filtration temperature
6. Change of product prescription
7. Change of filter sterilization conditions or sterilization methods
8. Change of filter manufacturer and manufacture process, or change of membrane material or filter structural composition